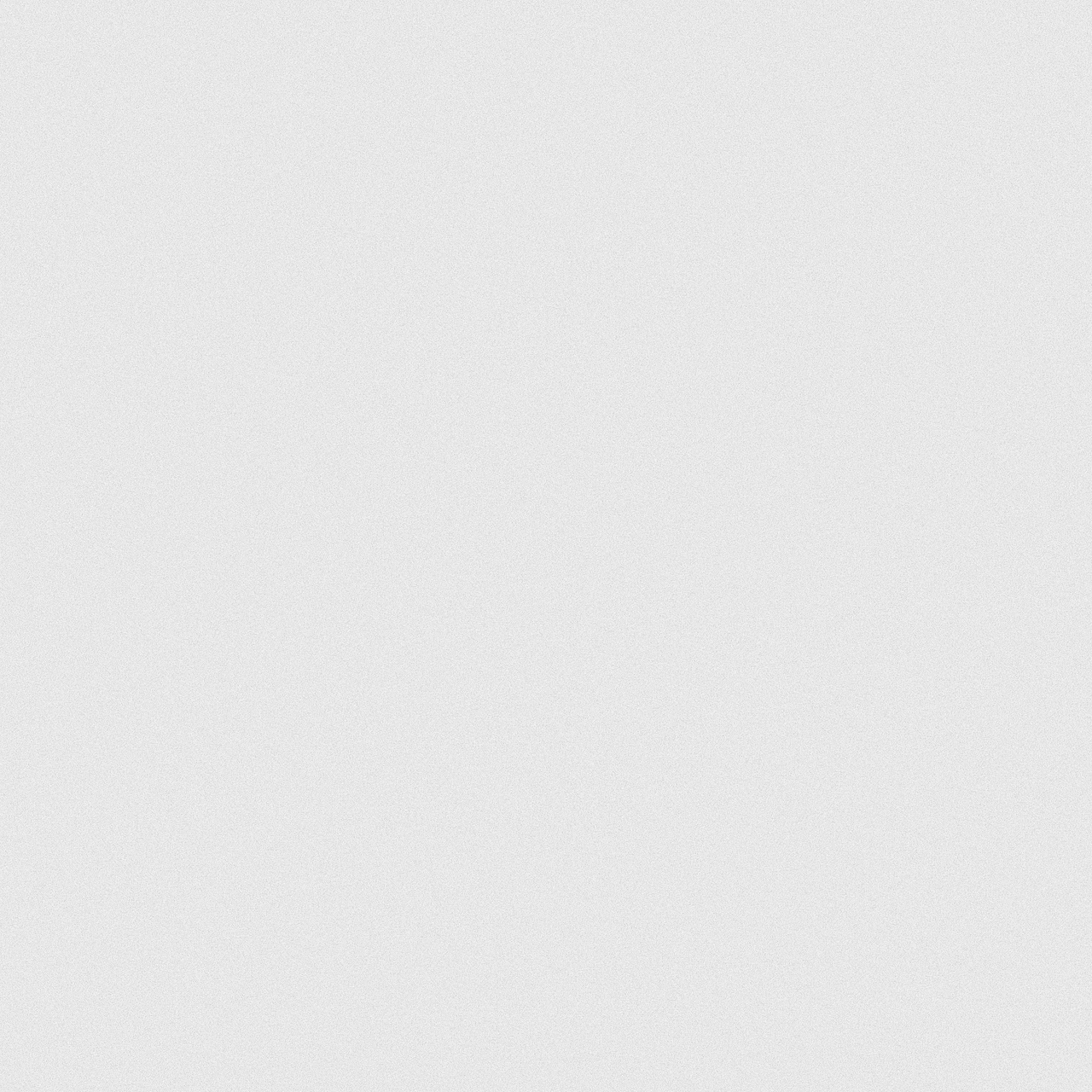

Analysis of A Biomimetic Path to Biofuels Production
Process Design and Technological Advancements
​
With this new technology we broke cellulose down to glucose without the need of supplying cellulase continuously. Thus, we were cutting down the raw material cost by increasing the capital cost by a little, and then the production load was maximized to get the lowest capital cost per gallon of ethanol produced. In addition, we did not need to worry about recycling the enzyme back anymore; since silica is a solid, the separation between the feed and catalyst was very easy, and we were able to easily strain all the solid catalyst back.
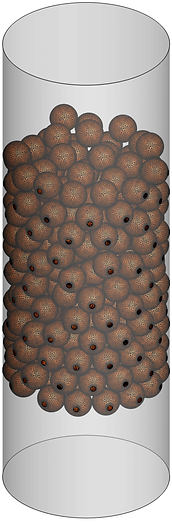
Not only was the stream pure since there was not a single trace of cellulase, the temperature of the reactor was more flexible, as it is now not constricted by the low breakdown temperature of cellulase. So now, a higher temperature was used and resulted in a higher rate of reaction.
​
However, there was a drawback, since silica catalyst was a surface catalyst: a modification to the reactor design was needed. A reactor that had a large surface area to reactor volume ratio was required. That was most likely be a PBR (Packed Bed Reactor) with porous silica sphere as the catalyst. A PBR created create a larger pressure drop compared to CSTR (Continuous Stirred Tank Reactor), thus a high pressure was needed in the feed, and also there was a significant energy loss due to the pressure drop.

These silica spheres act as catalysts for the depolymerization of cellulose.
Packed bed reactor (filled with silica spheres) is used to maintain a large surface area for hydrolysis.​​ ​​
naturalnspiration