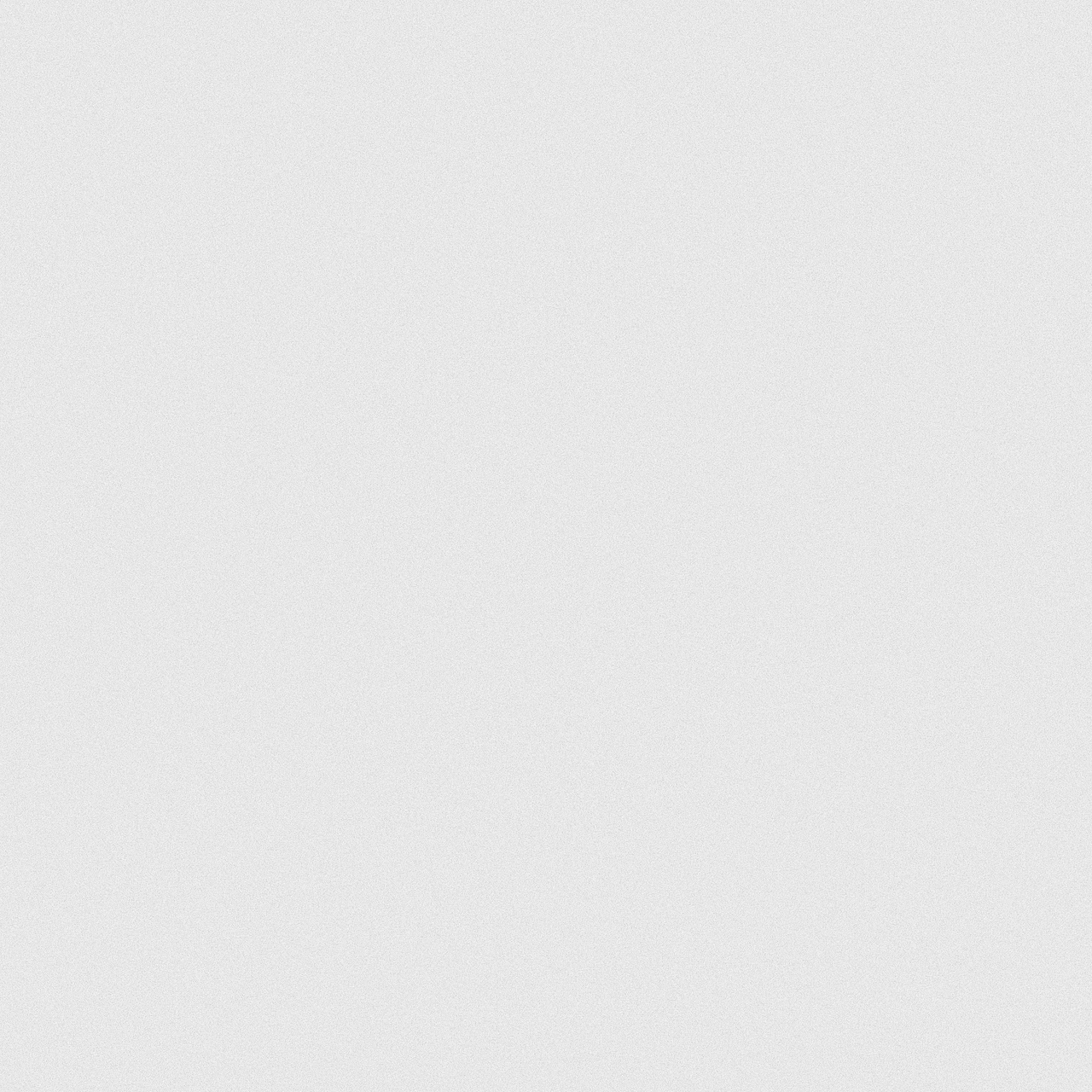

Analysis of A Biomimetic Path to Biofuels Production
Economic Analysis
The silica technology in the article addressed will only have an impact in the hydrolysis unit of the biomass to energy process. From this it follows that the only economic advantages that this new technology would offer would come from either capital costs of the hydrolysis reactor or its operating costs.
In this economic analysis several assumptions had to be made. It was assumed that the silica could perform equally well as the current enzyme technology (it currently only has only a 8% yield in the best conditions). In this is the inherent assumption that the cellulosic mixture would be able to be hydrolyzed like the glucan in the study. In all calculations properties of water were used and efficiencies were assumed to be 75% for all equipment (pumps and heat exchangers).
Overall this analysis is split up into three sections: Material, pumping, and heating.
Material
From several different sources in lecture the typical cost of enzymes was found to be between $10-25/kg. It is common knowledge that this is a big cost in the conversion of cellulose to ethanol. One possible advantage of silica hydrolysis is reducing this cost. The silica used in the article (Cab-o-sil M5) costs $70/kg. Based on this the process using silica would not be more economic. However if generic silica could be used and achieve similar yield the cost could be $0.1/kg. This is a significant cost savings and does not take into account the fact that silica can be recycled much more efficiently than enzymes can.
Pumping
One change that will have to be made to the process is that a PBR will have to be used instead of a CSTR (bioreactor) for hydrolysis. A well-known disadvantage of PBRs is that there is a significant pressure drop across the reactor that needs to be compensated for by increasing pumping power. To calculate the pressure drop over a PBR the Ergun equation is used.
The following values were used: H=10m, μ=0.001 Pa s, Dp=1 mm, ρ=1000 kg/m3 , v0=0.1 m/s. To calculate the void fraction, spherical particles were assumed and the equation below as used.
From this it was found that a pressure drop of 12.16 atm was present over the length of the PBR. Assuming 75% pump efficiency and the cost of energy to be $0.128/kWh, the total operating cost over a year would be $172,811. This is a cost that should be considered when thinking about employing a silica system.
Heating
According to the article the hydrolysis was carried out at a temperature of 105 oC, which is about twice the temperature of enzymatic hydrolysis reactors. On account of this heating costs will increase.
It was assumed that the yields were as follows: glucose->ethanol 50%, sugar solution-> glucose 80%, feedstock solution -> sugar solution 50%. Properites of water were used in all calculations. A starting temperature of 25 oC was also assumed. A simple energy relationship was used to calculate costs.
From here the previous energy price was used to get a heating cost of $0.178/ gal EtOH. This is 3.2 times the cost for a enzymatic process that runs at 50 oC. However is a heat exchanger is used at 75% efficiency the price can be reduced as follows, assuming a fermentation temperature of 37 oC.
This is the new price of heating per gallon of ethanol produced and is only 1.2 times the price of the enzymatic hydrolysis.
Conclusion
Based on the above calculations there are certain economic advantages and disadvantages to using silica for hydrolysis. All this depends on the performance of the silica. If the performance of the silica remains at its rather low yield there is no way the process will be more economical. More research and development on silica hydrolysis will have to be done to make this feasible.




naturalnspiration